TRANSFORMER MANUFACTURING
Partnering with the leading groups of industrial specialty manufacturing in Italy – vetted for their ability to produce to 100% custom requirements, specs and designs and respecting their minimum requirements for each unique transformer to create a schedule and budget that meets and exceeds the expectations and all testing & certifications of our American Electrical Companies as well as allows for our developer clients to confirm and proceed with their national development & construction schedules.
Our unique prowess and expertise in creating such complicated schedules for hundreds of elements under different umbrellas of production, from design to material to manufacture and delivery, allows GruppoGrid to apply this system in providing customized manufacturing of the variety of transformers, combining them into a comprehensive manufacturing schedule that extends to a multitude of sources & clients and contracts, with guaranteed quality & delivery dates.
We welcome the opportunity to explore how our production services can alleviate the stress and scheduling hurdles in today’s current situation for the manufacturing of transformers.
Contact us for an initial discussion with your requirements on specs and timelines.
The Backstory
Since 2000, Gruppo Italia has been providing production for all aspects of the architectural product world – directly to developers and builders, hoteliers & casinos and through leading architects & designers for luxury private client, multi-family residential & hospitality projects nationally. Such production includes furnishings, millwork, doors, flooring, stone, bathrooms, lighting, carpet and accessories, fully branded for the client/project or branded purely with MadeInItaly. Through a unique business model including strategic partnerships with select factories in Italy, Gruppo Italia expanded into manufacturing with a Private Label production model for national developers, hoteliers and distributors, creating “national standards”for brands, flags and designers.
In 2022, Gruppo Italia expanded & created an Industrial Fabrication facet, with first orders of custom aluminum fencing, various custom extruded components & fittings, customized machinery for various manufacturing of smaller batch fittings and the even more specialized material supply of Hyperpure Aluminum ingots.
Our heritage in the luxury and fully customized production has always included the custom extrusions of all hardware and most fittings, however the focus had been on the specialty projects that we accepted for our production provision, not the supply of industrial production for national distribution.
OPPORTUNITY & EXPANSION CREATED BY INTERNATIONAL SUPPLY CHAIN CRISIS
A local fencing company had come up against the supply chain woes of so many companies, and was unable to confirm production of the raw extrusions that they relied on for orders, business and expansion plans.
Studying their drawings and understanding the program of an initial requirement of 1 million pounds of 3 fencing products, our approach and preliminary steps proved to be far more than anything any of their other local suppliers had ever provided – and that million pounds grew to 3 million pounds, of 27 different elements for their leading sales products.
Our ability to guarantee delivery was met with a consistently “perfect production” – where not one ounce of the 3 million pounds was out of tolerance.
The GruppoApproach reporting systems far exceeds any expectations and is designed to also allow for coordinating all types of deliveries, and can dovetail with existing distribution, inventory and sales reporting systems ahead of delivery to insure accurate schedules and one stop storage for national distribution of our clients.
This new industrial dimension to Gruppo Italia’s offerings fulfills the complete circle of architectural products, and selling to American companies for distribution nationally as well as for specific projects.
The Gruppo DNA remains the same, only now extended into industrial production & still including the multitude of luxury products in the architectural & interior realm that Gruppo Italia and Made In Italy are instantly recognized for.
Every production that we take on has the same pillars of process…
Creating strategies and unique partnerships with our clients, from the onset of the design of a project or product, through our production engineering for any improvements on quality, longevity, scheduling &/or costing – and through a very detailed drawings and prototyping phase – for material and function – and with our production processes reported with confirmations, videos and photos through a proprietary system that can blend into a project schedule or sales & distribution matrix.
The logistics aspect of our production has always been as critical to our business as the initial design conversations – producing perfection must also be meticulously managed to insure that it arrives and is delivered on time and with full coordination and preparation to receive the production into a warehouse with inventory tagging in place for distribution & sales management tying into the varied client distribution systems, or coordination for direct delivery onto a construction site with all arrangements confirmed for ease & coordination to stage into place for installation services.
This new industrial facet of production may not provide the glamorous and sexy shots for our client weekly meetings, but are equally forceful, impressive and elicit awe at the magnitude of our machinery and the production lines, the overall size of the facilities, and the speed, perfection and technology mixing with the human touch for quality control approvals & processes.
Our fabrication of stone (blocks, slabs, fully cut & fabricated or material only) has the most similar “impact” in our reporting meetings when we share the realities of excavation – quarrying stone that was formed 60+million years ago, using machinery that is bigger than most homes! The reactions and amazement extends to wonder when we think back at the ancient Egyptians, Greeks & Romans in their use of stone, somehow with manual labor only, achieving perfection in dimension without the use of any lasers or heavy machinery – or electricity….
The Made In Italy factor seems to live and thrive in the Luxury universe – where it does indeed belong and leads the way with a heritage, a sense of design, and absolute demand for perfection and achieving excellence in all things within that Luxury universe, without exception.
However, in the not-so-sexy universe of heavy duty industrial manufacturing of everything, including the machinery itself – the Italian manufacturers constantly innovate and lead the way of Best in Class for practice and quality in this realm of extensive & diverse production.
Our ingenuity and demands for doing things better and achieving an unmatched excellence in quality, details, speed, efficiency for things we are designing or producing that which is designed and engineered by others provide a natural go-to for all things manufactured.
In specific regions of Italy, you will find the brain trust of engineering, production and ingenuity for materials, products and more. For example, and who knew? The Brain Trust for aluminum is a beautiful region outside of Milan – Brescia. Where we created a unique and powerful strategic partnership with an extrusion factory and achieved absolute perfection in the production of millions of pounds of fencing – with more being developed, tapping into that brain trust to improve existing products through the right engineering & production.
& NOW : GRUPPO GRID
When working with a leading national real estate developer, exploring TheGruppoApproach & extensive production offerings, focusing initially on the design & creation of a “standard” cabinetry & interior door collection that they can adjust in finish and some door details depending upon the current trend, designers vision and national region, we received a call from one of their Private Equity partners who recalled our aluminum story – and asked if there was any way we could source & provide the manufacturing of transformers.
Within a few weeks of extensive calls, zooms and a quick jaunt to Italy, GruppoGrid was formed. Realizing the magnitude and extensive requirement for the coordination of a multitude of specs, per region, per community and per electric company – a fully focused division is necessary to continue & expand as we serve the National Grid with the fabrication of fully custom to spec multitude of transformers, small and industrial.
The manufacturing of all things custom, is commonplace in Italy, where fully customized production is the norm and not an issue of concern for either budget or schedule – yet minimums may require a combining of production for various destinations.
And although Italy & the US are on different systems, every transformer is unique to the specs provided. Basically, the manufacturing of any transformer follows the exacting and precise specifications of each individual electrical company and provider.
Taking the specifications from a multitude of electrical companies, who are providing the electric for the residential communities nationally for this first client has led to conversations and studies of production requirements for the electrical companies outside of these specific developments, and include requirements for producing the largest of transformers for industrial use, including nuclear energy.
The Gruppo Approach remains the same – whether it be for a transformer, the machinery used to produce fittings, the aluminum framing for curtain wall systems on 100+story skyscrapers or a single extrusion of a top railing for terraces.
Our production schedules are typically backed into the clients’ requirements and abilities to receive – either at a warehouse, distribution center or individual project & location.
Even with our extrusions, we created a schedule that matched the clients’ receiving requirements since the enormity of our factories can typically produce the entire order in one run, clients can not manage receiving to our production capabilities. The loading of containers and sailing schedules allow for a continuous production, loading, sailing and receiving according to the realities of the clients here.
While we understand that the majority of the current transformer production is experiencing an unacceptable and unimaginable lead time, and impacting the schedule of turn overs for the residential developers nationally, so much so that the developers are doing all they can to cooperate, source and assist in every way to avoid a detrimental impact from this current crisis.
After these initial conversations, as we are underway in drawing review, study, testing and production on the first wave – we welcome the opportunities to review and discuss current and future needs with all electrical companies nationally. The more details and information we have, even if the requirements are not in the thousands of each style of transformer, we are working to create a system by which even the smaller quantities can be fulfilled, perhaps through minor changes to some design details to insure the minimum quantities for production are met, and then distributed through our precise network of freight logistics, including providing local distribution into multiple cities and states nationally as required.
CONTACT US
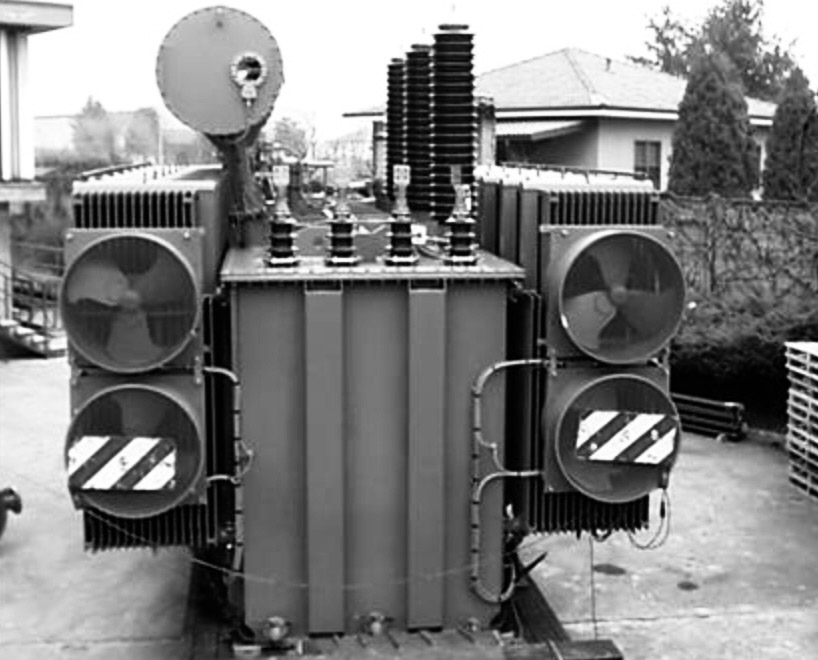
"*" indicates required fields